Knowing about various types of cement and their unique set of behaviors would allow you to opt the appropriate one for your construction needs. Actually the amount and proportion of various ingredients and components of cement are varied.
In my previous post, I have talked about Bogue’s compounds of cement. These compounds including C3S (Tri-calcium silicate), C2S (Di-Calcium Silicate), C3A (Tri-Calcium Aluminate) and (C4AF) Tetra-Calcium Alumino-ferite are basic components of cement. You can read in detail about function and percentage composition of each of these compound here.
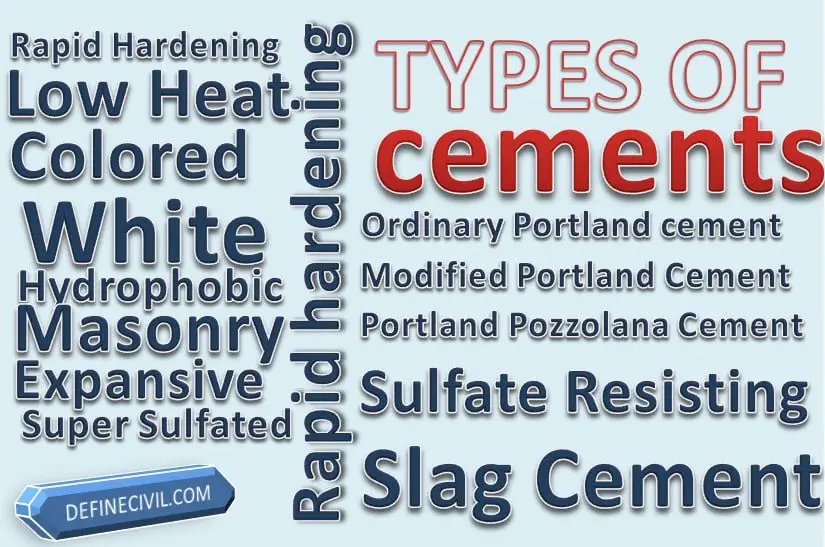
It is recommended for the readers that before knowing classification of cement get to know about the cement manufacturing process.
As a treat I am going to discuss that in one paragraph only; so if you’re short in time jump to main heading below of “types of cement” otherwise, continue below.
Cement acts as a binding agent in concrete that bonds together fine and coarse aggregate into a compact mass called concrete. In most of the cases, Portland cement is manufactured in a rotary kiln. The raw material includes sources of iron, alumina, silica and lime.
They are heated in the kiln at a clinkering temperature which is 2,500 to 2,800 degree Fahrenheit. The compact mass produced is thin grinded to a fine powder. During manufacturing, different supplementary cementing materials like gypsum or limestone are added to render required type of cement product.
- Ordinary Portland Cement
- Modified Portland Cement
- Portland Pozzolana Cement
- Sulphate Resisting Cement
- Portland Slag Cement (Portland Blast Furnance Slag Cement)
- Low Heat Cement
- Rapid Hardening Cement
- Colored Cement
- White Cement
- Oil Well Cement
- Hydrophobic Cement
- Masonry Cement
- High Alumina Cement
- Super Sulphated Cement
- Expansive Cement
- Air Entraining Cement
- Water proofing Portland cement
- Acid Resistant Portland Cement
- Anti-Bacterial Cement
- Quick Setting Cement or Rapid Setting Cement
Ordinary Portland Cement
Actually you already know about this type of cement; as this is the simplest of the all. In other words, we can call it a control type of cement as all others are derivatives of this type. It is actually the best type for ordinary concrete construction works like plastering, masonry works etc. For most of the house construction projects, the constructors still rely on this type of cement.
For ordinary circumstances, it offers a medium range of strength as well as the heat produced is of medium magnitude. You have to cure the concrete made by ordinary Portland cement for at least 7 days while it takes 7-28 days to achieve considerable strength.
The name “Portland” relates it to a stone i.e. Portland stone that was obtained from Isle of Portland, a place in England; because of similarity in greyish color. This type is actually patented and named by Joseph Aspdin who invented it and was worked by his son William Aspdin.
The ordinary Portland cement is categorized according to its grade. The grade defines the compressive strength of the concrete produced after lapse of 28 days. There are three common grades of Ordinary Portland type of cement; grade 33, 43 and grade 53.
Modified Portland Cement
A modified type Portland cement comprises of 1 to 30 percent by weight of a calcium halo-aluminate and calcium sulfate in to ordinary Portland cement. Cement produced in this way is cable of achieving high early set strength upon hydration.
So because of this characteristic, this type of cement can be used where formwork needs to be stripped early.
For most of precast structures and even while patching airport runways we require such a cement that can set quickly and develop less heat of hydration so for such applications, this modified Portland cement is the best option.
You can find more detail about its patent here.
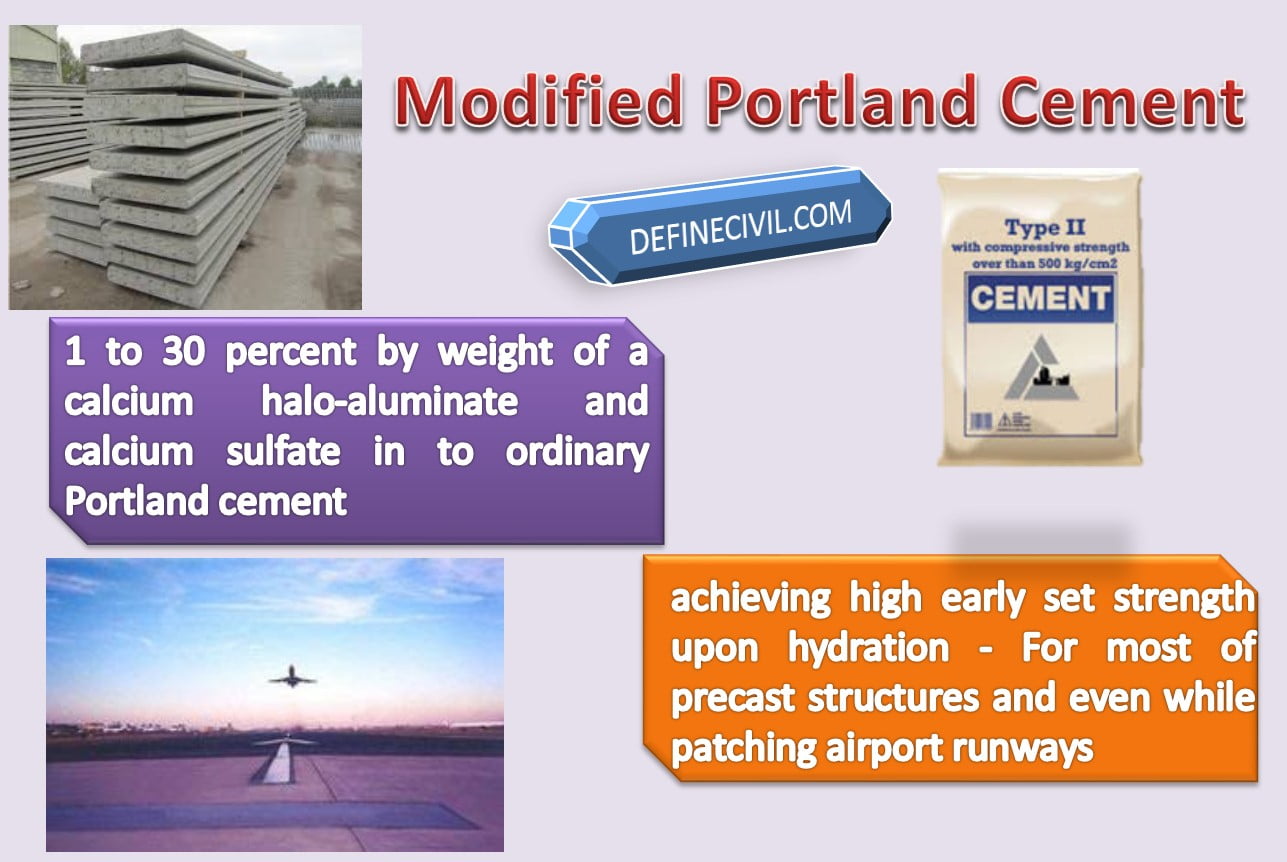
Portland Pozzolana Cement
In mass-concrete structures like dam or high rise buildings where controlling the heat of hydration is a challenge; this type of cement is very useful. Portland cement clinkers are grinded together with pozzolana while gypsum or calcium sulfate is added for its manufacturing. It offers enhanced resistance against attack of chemical agencies.
Pozzolana is actually a natural or artificial material having silica and alumina.
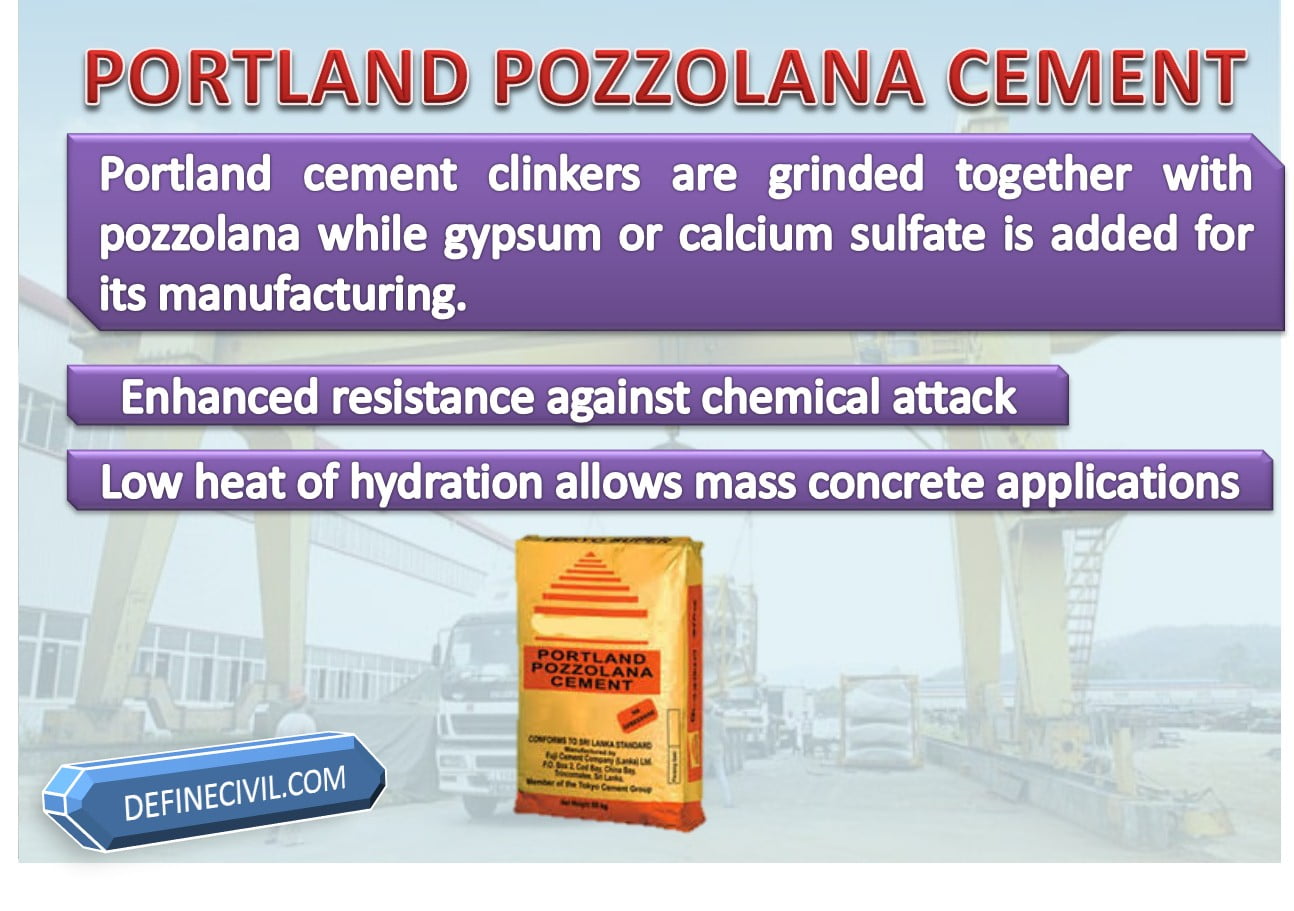
Sulphate Resisting Cement
Sulphate resisting cement or sulphate resisting Portland cement is a type of cement with low proportion of C3A (tri-calcium aluminate).
You might already know about sulfate attack; it is sometimes referred as cancer of concrete.
The reaction between C3A and gypsum (CaSO4.2H2O) produces calcium sulfoaluminate; but in most cases the calcium aluminate hydrate can also react with sulfate salts from environment that produces calcium sulfoaluminate. This cases an increase of 227 percent of cement matrix in hardened state that results in gradual disintegration.
It actually is produced by adjusting or limiting the proportion of C3A, SO3 content and C4AF component of cement. Because of high silicate content instead of C3A or C4AF; this cement can provide high strength but early strength is comparatively low. The heat developed is not much higher than that of low heat cement.
So; it is believed that the sulfate resisting cement is the ideal type of cement but as you have to adjust the proportions of the components; production of this type is not that easy and cheap.
The only disadvantage reported of this cement is corrosion of embedded reinforcement. C3A is reported to combine with chloride ions to form CaCl2 thereby reducing its concentration which was otherwise responsible for erosion of reinforcement.
Sulfate resisting cement is ideal for construction in grounds effected with saline groundwater or sea water.
In some applications; sulfate attack is also prevented by using mix designs rendering low permeability that would keep away the sulphate attack from the concrete matrix. The plastic or polythene sheet placed just above the soil from the foundation concrete also prevents sulphate attack as it acts as a barrier against entrance of sulphate ions.
Low Heat Cement
As the name abbreviates, this type of cement would limit the rate of heat evolution upon hydration of cement. The rise in temperature is obvious because of exothermic hydration reaction of cement. But this heat if left uncontrolled could lead to serious cracking and shrinkage.
This is one of the most important aspect in structures involving large concrete mass. Low heat cement is manufactured by lowering the rapid hydrating compounds like C3S and C3A. But reducing beyond a limit result in slower strength development and that’s why this type of cement is never recommended for thin concrete members.
Portland Pozzolana cement is sometimes regarded as a type of low heat cement.
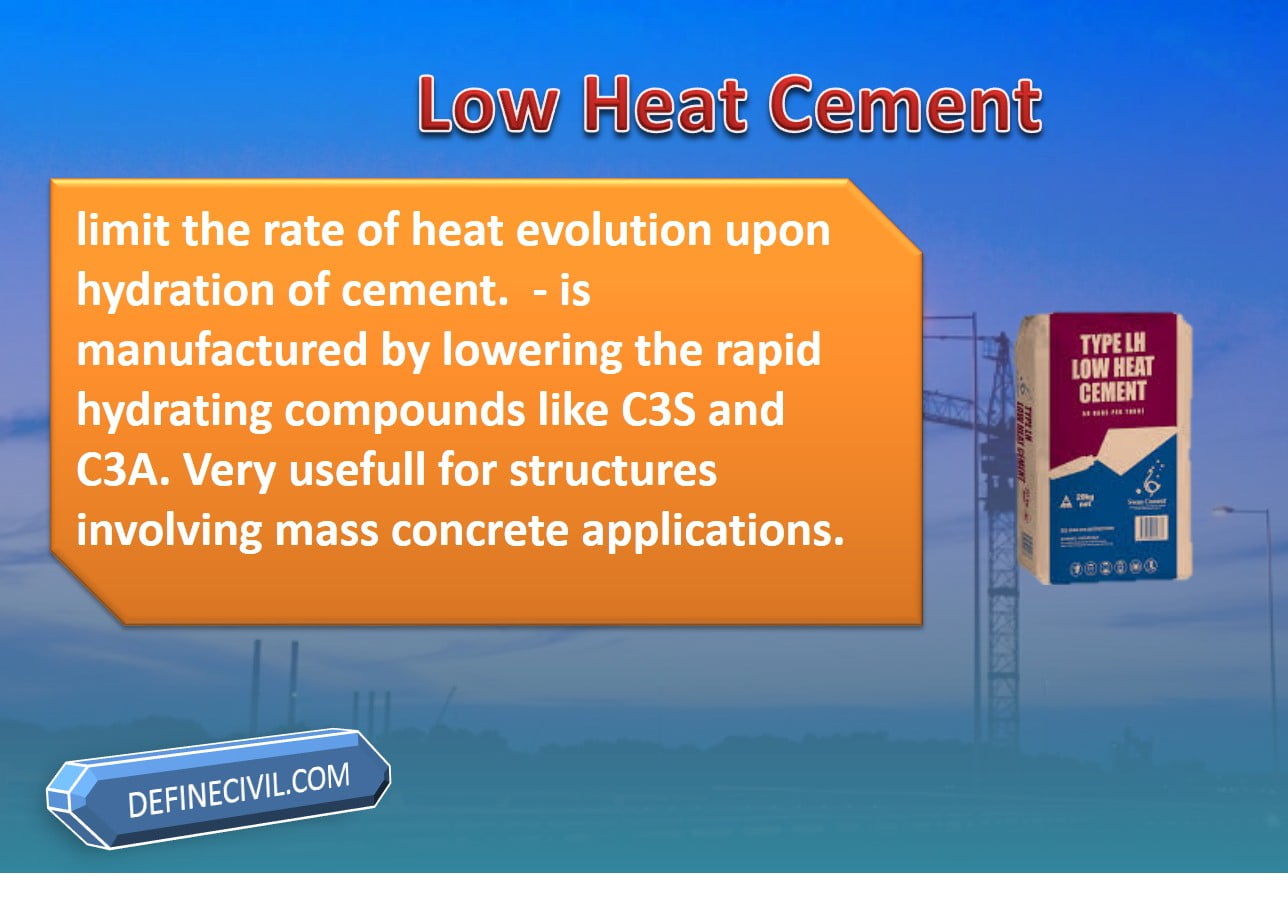
Portland Slag Cement (Portland Blast Furnace Slag Cement)
In iron industry during manufacturing of pig iron a waste product, similar in chemical composition to that of cement is produced. The mixture, although in different proportions, contains lime, silica and alumina along with some oxides like that of Portland cement. This mixture is called slag or blast furnace slag. Portland slag cement is manufactured by mixing Portland cement with ground granulated blast furnace slag.
Because of the presence of slag, the production of early heat is considerably reduced and this property is required in large mass of concrete. But because of low early heat, there is also an associated low early strength gain of such concrete.
One more advantage of blast furnace slag cement is its resistance to chemical attack and that makes it ideal for water retaining structures of marine structure.
It is comparatively economical than the ordinary Portland cement.
Rapid Hardening Cement
We know that the first 7 days’ strength of cement is because of C3S (Tri-Calcium Silicate). So if the proportion of C3S is increased we can increase the speed of hydration reaction.
So as the name implies, a rapid hardening cement is such a type of cement which quickly gains strength. According to one source, it can be stated that the strength gained by ordinary Portland cement in 7 days is equivalent to the strength gained by rapid hardening cement in 3 days; so there is a 7/3 ratio of strength gain.
Rapid hardening cement is actually high-early strength cement. But it is important to mention here that rate of hardening should not be confused with rate of setting. The rate of setting of both Rapid Hardening cement and Ordinary Portland cement is same.
In general circumstances, a higher percentage of C3S is 55 percent to 70 percent. In addition to this the cement clinkers are finely grinded as compared with that in ordinary Portland cement. The fineness of clinker ensures more area available for hydration reaction and thus rapid hardening phenomena is evolved.
This type of cement, finds its application in construction where formwork is to be removed early for re-use of where sufficient strength for further construction is wanted as quickly as practicable.
But this cement should not be used in mass concrete constructions because rapid hardening means increased rate of heat development which is destructive for mass concretes.
However, in areas of low temperatures where high rate of heat evolution is required rapid hardening cement could prove a satisfactory safeguard against early frost damage.
Similarly, in pre-cast member construction, like girders, pipes etc; rapid hardening cement is ideal.
White Cement
It’s a well-known fact that the grey color of cement is because of C4AF (tetra-calcium alumino ferrite) which is added during cement manufacturing to reduce the clinkering temperature.
White cement is only used for architectural or aesthetic purpose i.e. at the façade of a building or a member. Generally, the white cement is mixed with fine aggregate and, when required, with coarse aggregates.
Because of its low amount of soluble alkali, so you would also need not to worry about staining as in the case of ordinary Portland cement.
White Portland Cement is made from raw materials containing very little iron oxide (less than 0.3 percent by mass of clinker) and manganese oxide. Generally, china clay is used together with chalk or limestone. During manufacturing, oil or gas is used as fuel in a kiln instead of coal ash to avoid contamination.
But as I’ve told you that iron is used as a flux for lowering the clinkering temperature; so in its absence cryolite (sodium aluminium fluoride) is added.
This type of cement is not sutiable for structural concretes as its strength is somewhat slower than ordinary Portland cement.
Sometimes, the white cement is mixed with inorganic pigments to produce brightly colored concretes and mortars.
Colored Cement
In order to render a colored concrete; you can either use white color as a base for painting. But in alternate to that; pigments can also be added to cement. Iron oxide is well known to produce yellow, red, brown and black colors white chromic oxide produces green color.
A colored cement is obtained by intergrounding white cement with 2 to 10 percent of inorganic oxides as pigments. Some constructors name colored concrete as colcrete.
While mixing pigments; there are certain requirements as it should not cause problems for the admixture or even the air-entrainment.
Super Sulphated Cement
This type of cement is finer than the Portland cement and is made by intergrinding a mixture of granulated blast furnace slag (80-85%), calcium sulphate (10-15%), and Portland Cement (1-2%). Calcium sulphate is added in the form of dead-burnt gypsum or an hydrite).
The cement must be kept away from moist environments otherwise it would deteriorate rapidly.
This type of cement is very famous in Europe including Belgium, France and Germany.
One of the reason for its usage, is its high resistance to sea water or highest concentration of sulfates that are found in soil or ground water. The water/cement ratio should be kept more than 0.45.
Super sulfated cements are widely used for construction of sewers and in contaminated grounds. This type of cement also evolve very low heat of hydration and thus it also finds its application in mass concrete construction.
Air Entraining Cement
Air entraining cements are made by introducing air-entraining agents like resins, glues, sodium salts of sulfate with ordinary Portland cement. Air entrainment is a very important phenomenon for areas where freeze and thaw is liable to damage concrete.
The air bubbles introduced in the concrete matrix helps to absorb the stress induced upon freezing and increased volume. The air entraining cement is manufactured by mixing air entraining agents in the cement clinkers while grinding. It offers better workability and as the w/c ratio can be reduced because of air entrainment it can be used to achieve high strength mix designs.
It offers efficient resistance against sulphate attack as well as enhanced permeability of concrete.
Water Proofing Portland Cement
Water proofing Portland cement is used for specialized jobs when a water-repellent agent is mixed in the ordinary Portland cement. Sometimes it is termed as water-repellent cement. The additives are termed as hydrophobizing additives; which are water-insoluble like naphthenic acids, naphthenate soap, oleic acid, oxidized petrolatum, synthetic fatty-acid still residues etc.
These types of cement offers great frost resistance, greater imperviousness to water and are best suited for environments of heightened moisture conditions.
Acid Resistant Portland Cement
Construction of chemical industries and laboratories require acid resisting construction works. For such areas, acid resisting Portland cements are used.
High Alumina Cement
High Alumina cement is manufactured from raw materials of limestone and bauxite. Bauxite is obtained as residual deposit as a result of weathering of aluminum containing rocks in addition to hydrated alumina, oxides of iron and titanium with traces of silica.
High-Alumina Cement, as inferred by its name, contains higher percentage of alumina; usually about 40 percent each of alumina and lime in addition to several other compounds like ferrous and ferric oxides, silica, magnesia and other alkalis.
Due to the absence of Ca(OH)2 in hydrated high-alumina cement; it is well known for satisfactory resistance against sulfate attack. High-Alumina cement can also resist tolerably dilute solutions of acids found in industrial effluents. All the constructions near or in sea water are always constructed using high-alumina cement because of its stands up performance to sea water.
This type of cement can achieve strength at an extremely fast rate i.e. about 80% of its ultimate strength is achieved in 24 hours and you can strip formwork in about 6 to 8 hours. It has an increased compressive strength and thus it finds application in areas where high compressive strength is required.
It produces mixes which are more workable and with smooth finishes as compared with those of the ordinary Portland cement.
Hydrophobic Cement
Hydrophobic cement is a special type of water-repellent cement because of formation of a film around each particle of cement. It is manufactured by intergrinding Portland cement with 0.1 to 0.4 % of oleic acid. Stearic acid or pentachlorophenol. Because of these additions, grind-ability of clinker is increased and air entraining is also induced.
Hydrohobic cement is similar in appearance as ordinary Portland cement but has a musty small.
Masonry Cement
This is a specialized cement for the masonry works. It is manufactured by inter-grinding Portland cement with limestone and an air-entraining agent. Sometimes; slag or an inert filler is also added as ingredients.
This cement produces more plastic mortar with enhanced water-retaining properties that leads to lower shrinkage. Although the strength of this type of cement is lower; but this is not a concern in masonry works.
But this cement should not be used in any structural concrete works.
Expansive Cement
One of a major concern faced by constructors in cement construction works is its uncontrolled shrinkage which if left unattended could be disastrous for the structural integrity. For such situations, expansive cement is for your rescue.
Expansive cement, is valuable in structures where reducing in shrinkage cracking is important like bridge decks, pavement slabs or water retaining or storing facilities.
In most situations, an expanding agent is mixed with Portland cement. In modern type of expansive cements, source of reactive aluminate are used that combine with sulfates of Portland cement to form expansive ettringite.
The controlled formation of ettringite in early days after placing of concrete is used to achieve a shrinkage compensating effect.
Oil Well Cement
Petroleum industry during exploratory drilling require to grout holes with depths in excess of 10,000 meters in to the earth’s crust where increased values of pressure and temperature are expected. The temperature can exceed 1500C and pressure around 100 MPa. So for such specialized applications; this type of cement is used.
Oil-well cement is prepared by mixing Portland cement with specialized agents to modify its properties as required by drilling operations. The cements are made to reach distant locations without getting set but to gain strength rapidly. It contains retarders or accelerators when required along with particular fineness as well as friction reducers and light weight additives.
Anti-Bacterial Cement
This is also a specialized type of cement. Anti-bacterial cement is manufactured by mixing Portland cement with an anti-bacterial agent that prevents microbiological fermentation.
Mostly in food processing plants leaching out of cement happens by acids followed by fermentation caused by bacteria in presence of moisture. For such situations anti-bacterial cements are used.
This specialized cement also finds its applications in swimming pools and similar places where bacteria or fungi are present.
Rapid Setting Cement
Quick Setting Cement or Rapid Setting cement must not be confused with rapid-hardening cement. Hardening is a term related to strength gain while setting is something relating to workability of cement. Many people get confused about these two terms but the difference is explained above for you.
Rapid Setting or quick setting as the name implies could allow you to remove or strip formwork early but you could not allow the serviceability of the structure immediately i.e. in case of a rigid pavement you could not allow movement of traffic as early with rapid setting cement.
Rapid Setting Cement is that having initial setting time of even less than 10 minutes while final setting can go up to 5 hours. This type of cement is used where quick setting is required like in mine construction works.
Summary
[su_table responsive=”yes”]
Sr.No. | Type of Cement | Composition & characteristics | Application |
1 | Ordinary Portland Cement | Usual composition of 4 component of Bogues compounds. | Used for ordinary concrete construction works like plastering, masonry etc. |
2 | Modified Portland Cement | Contains calcium halo-aluminate and calcium sulfate – cable of achieving high early strength with less heat of hydration | Popular for precast structures, patching airport runways. |
3 | Portland Pozzolana Cement | Have added pozzolana along with gypsum or calcium sulfate – controlled heat of hydration and enhanced resistance against chemicals | Best for high rise buildings and mass-concrete structures like dam. |
4 | Sulphate Resisting Cement | Have lower proportion of C3A (tri-calcium aluminate) and high silicate content. – can produce high strength and resistance against sulphate attack | Ideal cement for grounds effected with saline groundwater or sea water. |
5 | Portland Slag Cement | ||
6 | Low Heat Cement | Produced by lowering rapid hydrating compounds like C3S and C3A – limits the rate of heat evolution | Ideal for mass concrete structures where low heat of hydration is required. |
7 | Rapid Hardening Cement | It has increased proportion of C3S – it quickly gains strength | Usage of precast structure or roadworks where early servicing of the structure is required. |
8 | Colored Cement | Made by intergrinding while cement with 2 to 10 percent of inorganic oxides as pigments. | Are used as base for paint walls or for finishing works. |
9 | White Cement | While cement has reduced percentage of C4AF – very little iron and manganese oxide. | Not recommended for structural concrete but is used only for architectural or aesthetic purpose at façade of a building. |
10 | Oil Well Cement | It contains retarders or accelerators along with specialized agents for making cement to reach distant locations without early set. | This is used in exploratory drilling or petroleum industry – and for petroleum industry works. |
11 | Hydrophobic Cement | Water-repellent cement made by mixing 0.1 to 0.4 % of oleic acid, stearic or pentachlorophenol. | Use in water front or water retaining structures where permeability is to be minimized. |
12 | Masonry Cement | Used by mixing OPC with limestone and air-entraining agent. | Used for masonry works – not recommended for structural concrete works. |
13 | High Alumina Cement | Have high percentage of alumina – manufactured by mixing limestone and bauxite. | Very well known for satisfactory resistance against sulfate attack. Resists against dilute solutions of acids. |
14 | Super Sulphated Cement | Made by intergrinding granulated blas furnace slag, calcium sulphate, Portland cement. – produces very low heat of hydration | Famous in Europe – used for high resistance to sea water where there is high concentration of sulfates. |
15 | Expansive Cement | Expanding agents are mixed with Portland cement – source of reative aluminate are mixed with sulfates of Portland cement – reducing shrinkage cracking | Are very useful in important structure like bridge decks, pavement slabs or water retaining structures. |
16 | Air Entraining Cement | Air entraining agents like resins, glues, sodium slats are added with ordinary Portland cement – can produce air entrainment | Best for concrete works in freeze thaw environment – better workability and high strength concrete. |
17 | Water Proofing Portland Cement | Water repellent agents such as naphthenic acids, soap or oleic acid etc are mixed. | Offer great frost resistance and imperviousness to water. |
18 | Acid Resisting Portland Cement | Acid resisting agents are mixed – | Best for construction of chemical laboratories. |
19 | Anti-Bacterial Cement | Mixed with anti-bactarial agent that prevents microbiological fermentation. | Used in swimming pools and food processing plant constructions. |
20 | Quick Setting Cement | Accelerating admixtures are added and cement clinkers are grinded with aluminum sulphates. | Used where quick setting is required like in mine construction. |
[/su_table]
Closing Note.
There are many exciting features about cement and concrete construction out there. I recommend you bookmark this page as it is your resource for cements types and various features in construction.
There are many types of cement used in construction industry and you may find yourself in a situation where it could be difficult for you to decide the right option for your needs and demands. So I’ve tried to cover all and have crafted this super-amazing long piece of content for you.
Don’t forget to visit the related articles as they would surely enhance your understanding and knowledge about this field.