Whether you’re into a concrete project or want some material to fill under the foundation or floor, different types of aggregates are useful. All these types have different function and purpose so it is crucial to select a type that does along your project requirements.
Aggregate is a broad term for fine to coarse fragments of rock pieces used as filler in concrete or backfill material during road or dam construction. Their applications range from use in concrete to use in highway and other construction projects.
In concrete, aggregates act as filler i.e. volume occupying ingredient and provide strength against abrasion and erosion.
Furthermore, aggregates impart durability and toughness to concrete. In highways, aggregates are used in sub-base and base course as load transferring medium and in pavement they combine with asphalt to form asphalt concrete.
The use of aggregate in construction is diverse. They are also used in manufacturing tuff tiles and other related material.
In this article, we will discuss about properties of construction aggregate, their suitability in construction, and classification according to different factors. Our primary focus will be on coarse aggregate.
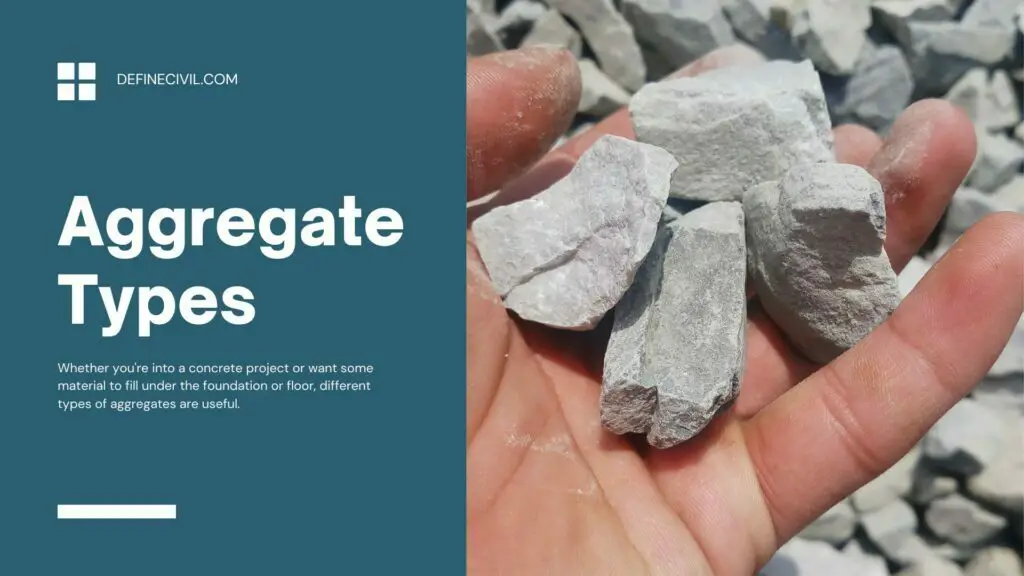
Properties of Aggregate for Use in Construction
There are certain parameters that must be fulfilled by aggregate for use in construction projects. So, here’re qualities of good aggregates:
- Aggregate should have sufficient hardness and toughness. It should not scratch easily and should not break under the impact of loads.
- It should be chemically inert. It should not react with other constituent material.
- It should be free from deleterious material. These impurities react with other constituents and form unwanted compounds. Efflorescence is an example of such reaction.
- It should not contain high quantity of silica. A high quantity of silica triggers alkali-silica reaction which leads to spalling of concrete and ultimately it loses all its strength.
- It should have adequate specific gravity. Generally, for construction purposes, a good aggregate should have a specific gravity equal to or greater than 2.7.
- The percentage of flaky particles (those having one dimension greater than 3/5th of their average size) should not be greater than 15%.
- The aggregate should have minimum permeability. Highly permeable aggregates absorb water and cause deterioration.
- It should be able to produce a workable plastic mix. The mix formed by adding aggregate should neither be harsh nor sticky.
Classification of Aggregates
Aggregates are classified according to multiple factors. We will discuss each of them.
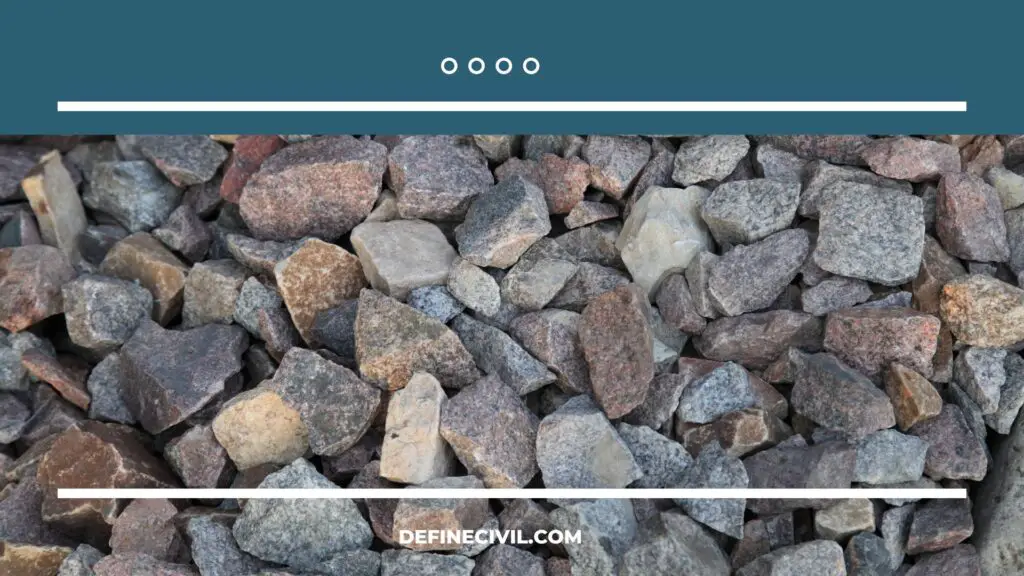
Classification Based on Size
Fine Aggregate
Fine aggregates are those which pass through sieve No.4 and are retained on sieve No.200. The size of these aggregates is between 4.75mm and 0.075mm. The particle size distribution of these particles is determined by sieve analysis. The most common example of such aggregate is sand.
Coarse Aggregate
Coarse aggregates are those which are retained on sieve No.4. The size of these aggregates is equal to or greater than 4.75mm. Crushed rock is an example of coarse aggregate when crushed to specific sizes. Gravel is another example of naturally occurring coarse aggregate.
Classification Based on Density or weight
– Lightweight Aggregate
Lightweight aggregates have low density. These are the aggregates having unit weight up to 12kN/m3. These are commonly used to manufacture structural concrete and masonry units for reduction of self-weight of concrete. In addition to that, these aggregates are used for fire and acoustic insulation. Lightweight concrete blocks are also manufactured using these aggregates.
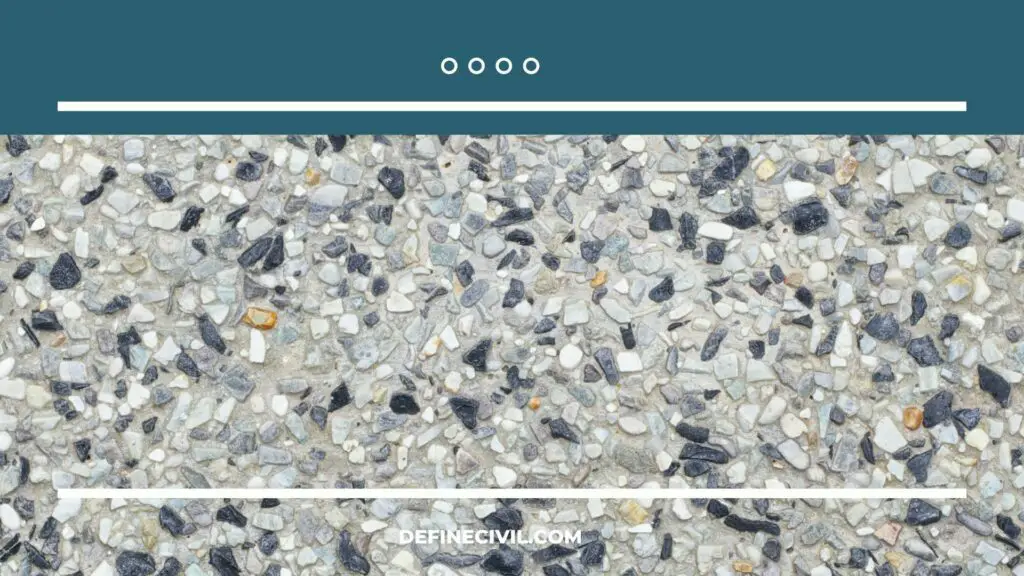
– Medium Density Aggregate
These are the most frequently used aggregates for general construction purposes. Their density varies from 23-26kN/m3. Sands and gravels, crushed rocks such as granite, basalt, sandstone, slate, and limestone are common examples. The specific gravity of these aggregates is between 2.5 and 2.7. These aggregates are commonly used to manufacture concrete.
– Heavyweight Aggregate
Aggregates having specifically gravities ranging from 2.8 to 2.9 and unit weights from 28 to 29kN/m3, are called heavyweight aggregates. These aggregates are used in the manufacture of heavy weight concrete. This concrete is effective as a radiation shield. Examples of these aggregates are magnetite, barite, and scrap iron.
Classification Based on Origin
– Natural Aggregate
These are naturally occurring aggregates. These aggregates do not require any processing nor are they results of some other process. These aggregates are extracted from large rock formations through open excavation. After that, excavated rock is further reduced to required sizes using mechanical crushing. Examples of these aggregates are pit sand, sand from river beds, naturally occurring gravel, and aggregates from different rock formations such as basalt, limestone, etc.
Also Read: 14 Types of Stones in building construction (composition & properties)
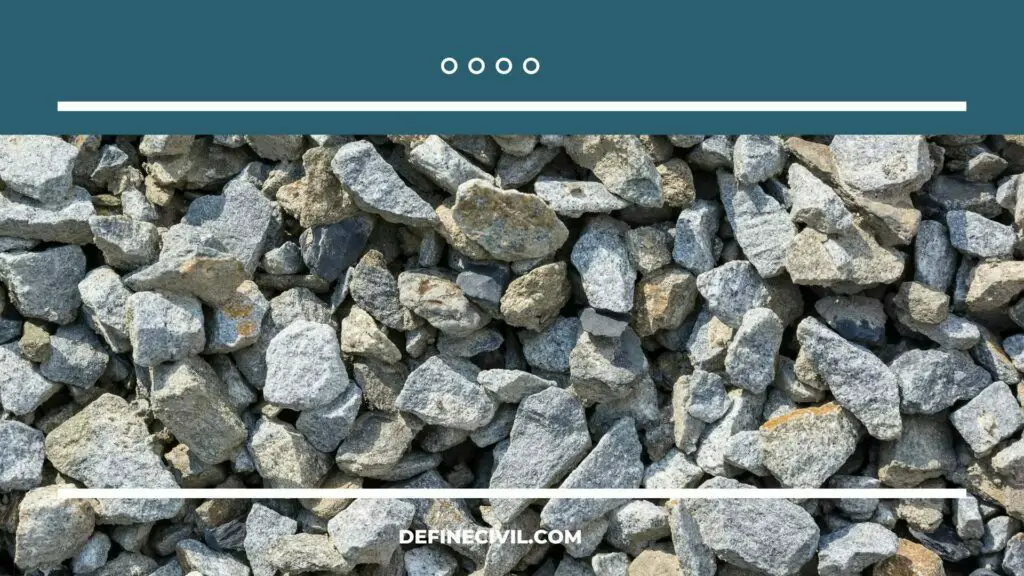
– Artificial/Manufactured Aggregate
Manufactured aggregate is usually the by-product of other manufacturing industries. These aggregates do not occur in natural forms. Examples of these aggregates are fly ash, silica fume, and blast furnace slag. There are other various varieties of these aggregates.
Classification based on shape
Shape of aggregate does play a vital role in defining the overall mechanical properties of aggregate. That’s why we commonly use a lab test to check the flakiness and elongation of aggregates. The shape also impacts the workability of concrete. Natural aggregates mostly have rounded shape due to erosion or weathering. Here’re some common aggregate types based on shape:
Rounded Aggregates
These are natural aggregate shape available at the bed of rivers and other flowing water bodies. This seashore gravel is not only a good choice for ornamental purpose but can also find application in concrete where workability is required. Because of least resistance against particles, the aggregate are also performing in low water-cement ratio.
However, rounded aggregates are not suitable for high-strength concrete because of poor interlocking strength and weak bond behavior.
Irregular Aggregate
When you don’t get aggregates from a single source, you get the irregular aggregates. You’ll find these aggregates in the shape of pit sands and gravels. Because of irregular shape they have lesser amount of voids when placed and shows lesser workability than rounded aggregates. But the still, these aggregates are not a preferred choice for high-strength bond concrete.
Angular Aggregate
As the name implies, angular aggregates has sharp and well defined edges. They’re mostly obtained by crushing rocks in primary and secondary crushers in different sizes like 38 mm, 19 mm, and 5 to 8mm. Because of angular shape and good interlocking properties, it offers lesser workability but still show good bond strength. They’re in fact the most common types of aggregates we use in construction projects – concrete or filling.
Flaky aggregate
Flaky gravels are another shape of aggregate that are like slim and smart. They have less thickness when compared to the length or width. By definition, the gravel that has least dimension less than 60% of its mean dimension then that of aggregates are flaky.
Elongated
Here the length of aggregate is a dominating factor. That means the length is larger compared to the width or the thickness at the same time. So, if the aggregate length is greater than 80% of its mean dimension, we can call the aggregate as elongated aggregates.
Flaky and elongated aggregate
If the aggregates have both characteristics of elongation and flakiness, it is termed as flaky and elongated aggregate. It means the length is larger than its width while the width is larger than the thickness.
Also Read: Cement Concrete Calculator – Online calculate cement sand and aggregate