Bogues compounds are responsible for initial setting of the cement grout. These compounds have been researched extensively by an American chemist named Rober Herman Bogue (R.H. Bogue) who is well known for his books on The Chemistry of Portland Cement and the Chemistry and Technology of Gelatin and Glue.
After his extensive research, Bogue has devised a calculation system that assumes four main minerals in cement clinker responsible for cementitious properties.
With these calculations one can derive the optimal proportion of the mineral composites to estimate the amount of uncombined free lime.
By the process of hydration, we know that each mineral constituent of cement, after reaction with water, takes part in strengthening of concrete (a mixture of cement, aggregate and water).
Bogues through his calculations has explained that varying the proportions of these ingredients can produce different properties and characteristics of cement composite.
What is bogues compounds?
Bogues compounds are complex compounds formed during burning process that are responsible for setting and hydration of cement. When water is mixed in cement, it reacts to form complex compounds simply called as bogues compounds.
Here’re bogues compounds with composition and chemical formula:
Bogue’s Compounds | Composition %age | Chemical Formula |
Tricalcium Silicate | 30-50 | C3S |
Dicalcium Silicate | 20-45 | C2S |
Tricalcium Aluminate | 8-12 | C3A |
Tetra-Calcium Alumino Ferrite | 6-10 | C4Af |
Also Read: Fineness test of cement – A very informative Article – Read here
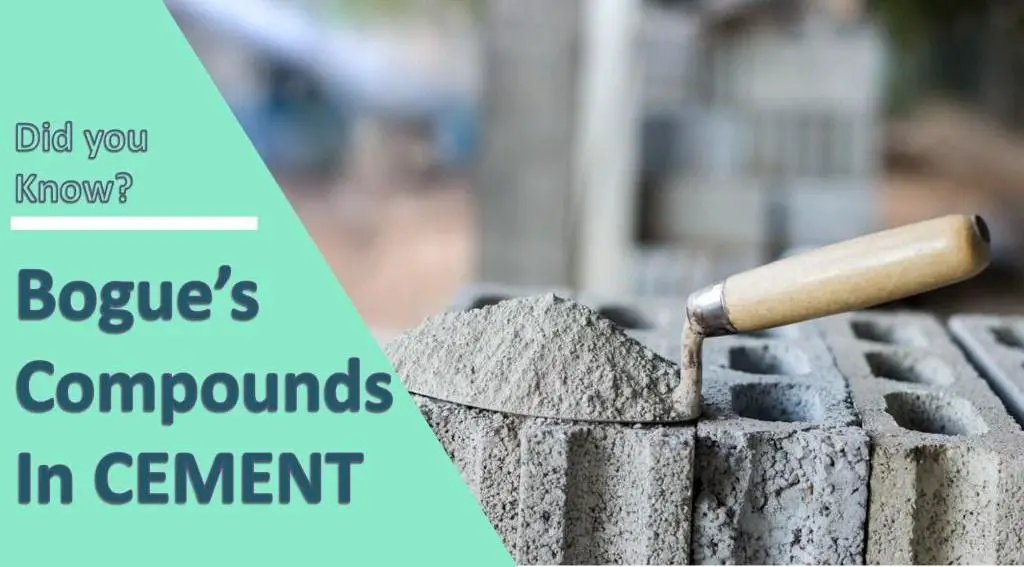
Definition of Bogues Compounds of cement
So, honoring his work, these compounds are named after him and thus the primary compounds or constituents of Portland cement responsible for setting of cement paste are called Bogues compounds.
Classification or Types of Bogue’s Compounds
Following are the four Bogues compounds, these are also the four main ingredients of cement
- Tri-calcium Silicate
- Di-Calcium Silicate
- Tri-Calcium Aluminate
- Tetra-Calcium Alumino Ferite
I would now be explaining all of these Bogues compounds in cement, how their proportion may change the properties of cement paste and generally in how much proportion they are added or present in cement clinker.
Also Read: Specific Gravity of cement – A very informative Article – Read here
Significance of Bogues Compound of Cement / Concrete Properties
Let’s now explore the role of various bogue’s compound in cement:
- Tri-calcium Silicate
I am starting from Tri-Calcium Silicate, also written as C3S; because comparatively it is the constituent that is present in great percentage i.e. 30-50%.
It is chemically expressed as 3CaO.SiO2.
About 50-60% of the cement paste strength is owing to the presence and proportion of tri-calcium silicate. The strength of the first 7 days (a week) of concrete pour is because of tri-calcium silicate.
Upon addition of water to the cement paste, the tri-calcium silicate reacts with water in an exothermic hydration reaction producing calcium and hydroxide ions.
Once the system is saturated with ions, the calcium hydroxide starts of crystallize thereby producing calcium silicate hydrate simultaneously.
These hydrate crystals grow thicker thereby reducing the speed of the reaction because of difficulty for the water molecules to reach un-hydrated tri-calcium silicate. In this way after crystallization the hardened cement paste is produced.
In concrete structures like pre-caste members or pre-fabricated construction, we want the concrete to set quickly and by increasing the proportion of tri-calcium silicate we can achieve this by producing a rapid hardening cement.
Same is the case for the cold weather concrete construction.
Also Read : Different grades of concrete – A very informative Article – Read here
- Di-Calcium Silicate
Comparative to tri-calcium silicate, the di-calcium silicate is less reactive. It is also written as C2S and is chemically expressed as 2CaO.SiO2. It is second most abundant constituent of cement composite; as it is present in 20-45%.
The Di-calcium silicate reacts with water, a bit slower, but in similar manner as tri-calcium silicate. This is also an exothermic reaction but heat produced in it is way less than that of previous explained reaction.
The di-calcium silicate, as is responsible for strength at later stage i.e. after 7 days to 1 years, is very important for hydraulic structures as well as bridges that needs strength after years of service and detrimental effects.
Similarly, for constructions where less heat of hydration is mandatory, like in low heat cement, the proportion of di-calcium silicate is adjusted accordingly.
Also Read: Harsh Concrete – Reasons and How to improve harsh concrete mix
Heat of Hydration
Do you know: The heat of hydration of bogues compound is 865 J/Cal. C4AF hydrates in large fraction early during setting while the last one to be hydrated is C2S. So, we can write the compounds in decreasing order of hydration as C4AF, C3A, C3S, and C2S.
- Tri-Calcium Aluminate
It is present in 8-12% of the cement composite. Tri-calcium aluminate is also written as C3A and is chemically expressed as 3CaO.Al2O3.
It is produced within 24 hours after mixing of water and the early strength of the cement paste is because of tri-calcium aluminate.
In areas where a quick set is required like in grouting of drain holes or to avoid water leakage the amount of tri-calcium aluminate is increased.
But as it produces a large amount of heat of hydration, it must not be used much in projects of mass concrete like in Roller Compacted Concrete hydraulic or water retaining structures.
The excessive heat of hydration if remained unattended will result in excessive cracking deteriorating the structural integrity and for this reason fly ash is added in the mixture.
Also Read: Soundness test of cement – A very informative Article – Read here
One of a very unique benefit of its presence is that it avoids the corrosion of steel rebars because of its chemical nature.
Tri-calcium aluminate combines with chloride ions to form CaCl2 thereby decreasing the concentration of chloride responsible for erosion of steel reinforcement. However, this aspect of C3A in cement type I and III are still being explored by the scientist.
One of the most destructive impact of C3A on cement is to make it prone to sulfate attack in environments rich in sulfates. As the reaction of C3A with water is very fast that leads to an immediate solidifying of cement paste called flash set or false set.
To avoid this gypsum, (calcium sulfate) also termed as Plaster of Paris, is added in proportion of 4-8 % during grinding the cement clinker.
But this mixture of gypsum and C3A together forms ettringite which later becomes monosulfate. This monosulfate then reacts with sulfate in the external environment in a strongly expansive reaction causing an intense material degradation.
- Tetra Calcium Alumino Ferrite
Tetra Calcium Alumino Ferrite is present as 6-10% in cement composite. It is also written as C4AF and is chemically expressed as 4CaO.Al2O3.Fe2O3.
Tetra calcium alumino ferrite is actually not a compound that aids in the strength of cement. During hydration reaction of cement, it forms a hydrated iron oxide gel in a fast reaction producing enough heat but the reaction slows down once calcium alumioferrite crystals are formed.
But its addition is made to aid cement manufacturing process by providing a lower clinkering temperature. Beside this it acts as a filler cement to make it economical and also gives cement its greyish tint which is loved by the constructors.
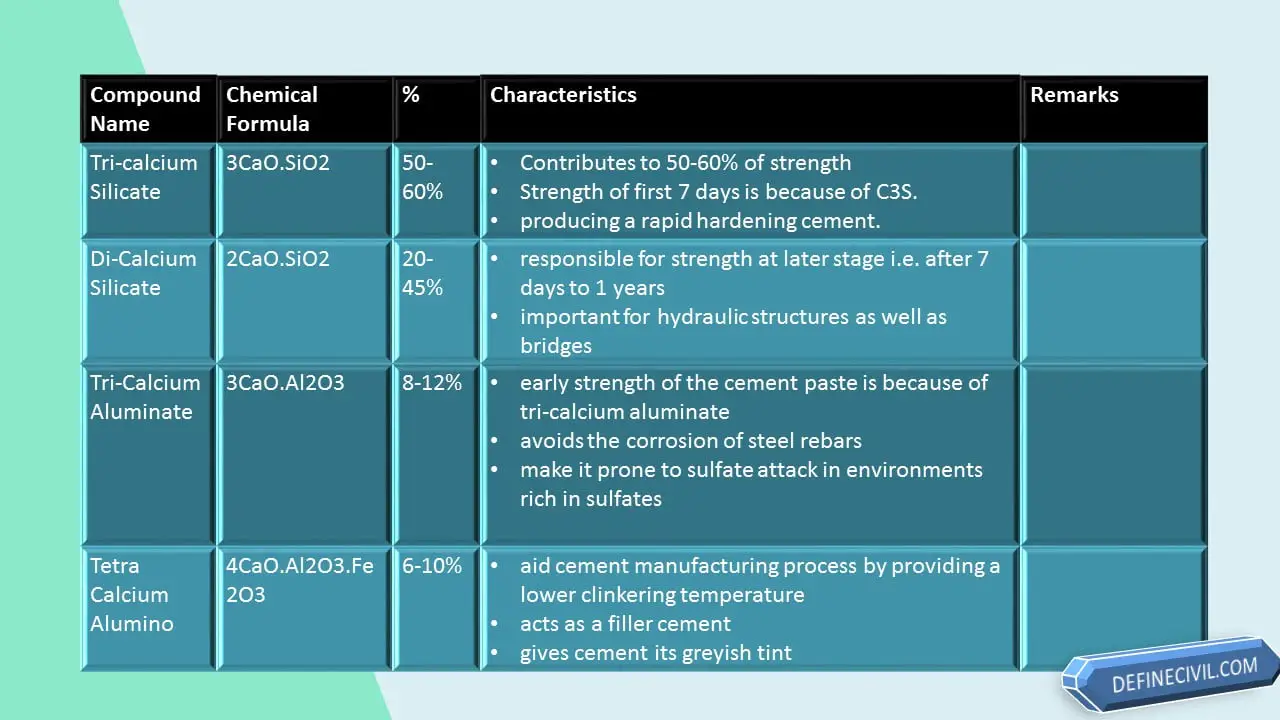
Also Read: Classification of cement- A very informative Article – Read here
FAQs
Well, here’re some of the frequently asked questions by our fans and followers:
- Which bogue’s compound provide ultimate strength to cement?
- Well, if you’re looking for a cement that gains ultimate strength in just 24 hours, you have to increase the content of Calcium Aluminate (CaO.Al2O3). Tricalcium silicate just provide the ultimate strength of cement upto 50%.
In Conclusion
All the bogue’s compounds have their own significance in enhancing properties of cement to make it strong, durable and enhancing its resistance to detrimental effects of the environment.
But as we have seen, all the constituents have pros and cons so a very careful estimation and approximation is required which is well explained in bogue’s calcuations.
We would also like to pay tribute to Bogue as his calculations are the base points for the cement manufacturing industry.