Rapid hardening cement is a particular type of cement that is used in exceptional cases of concrete pouring. As the name implies, rapid hardening cement needs the shortest time to set up and consolidate. It achieves higher strength on lesser days.
With such, it can attain seven days strength in only three days. You can also relate rapid hardening cement to high-early strength Portland cement in the classification.
So, in today’s article, I will discuss the composition, properties, advantages, disadvantages, and comparison.
Let’s get started:
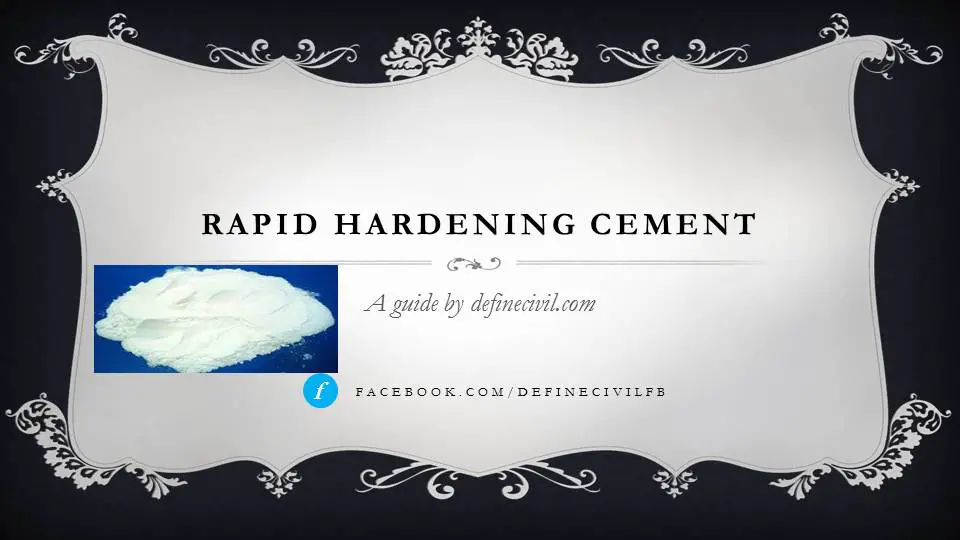
What is Rapid hardening cement? – The Definition
Rapid hardening cement, also abbreviated as RHC, hardens quickly and produces excellent strength. This early attainment of strength is mainly due to the high proportion of lime content.
This higher percentage of lime is the only difference between rapid hardening cement with ordinary Portland cement. Alongside, the RHC also has more refinement of grinding. These finer cement particles help for quick strength and hydration reaction.
Recommended for you: Fineness of Cement
The finer the cement particles are, the more surface area there is for water to interact on, resulting in faster hydration. As a result, rapid hardening cement produces substantially more heat of hydration in the initial stages.
Composition of Rapid Hardening Cement
Rapid Hardening cement contains the following proportions of Bogue’s compounds of ingredients:
- 60% Tricalcium silicate (C3S) – This is the main ingredient we use as raw material. This lime is responsible for the rapid gaining of high early strength.
- 15% Dicalcium silicate (C2S),
- 10% Tricalcium aluminate (C3A) and.
- 8% Tetracalcium aluminoferrite
Please Note: The above percentages of ingredients are based on the total weight of cement.
Recommended for you: Water Cement Ratio
- It attains early strength due to lime. We include a large proportion of lime grounded finer than ordinary cement. That’s the reason why it attains early strength faster than OPC (Ordinary Portland cement).
- The initial setting time for this type of cement is not less than 30 minutes. It solidifies within 30 minutes.
- However, the final setting time is not more than 600 minutes. Anyhow, the cement attains considerable hardness at this stage.
- As explained above, it has a high percentage of lime.
Uses of Rapid Hardening Cement:
All the uses of the rapid hardening cement are due to the early attainment of strength. Following are the rapid hardening cement uses:
- Rapid hardening cement is the only solution when you have fewer formwork sets, and you need to speed things up. It allows you to quickly remove the formwork and reuse the same in some other pour.
- Most construction sites rely on RHC, where a high amount of strength is required to bear the stress. Like in the case of bridges or road flyovers.
- It is utilized to construct road pavements where it’s critical to get the route open to transport rapidly.
- As the removal of molds is swift thus companies that produce composite materials such as concrete slabs, posts, power poles, barricades, fences, and many more, use RHC.
- Since the quick increase of temperature during hydration preserves the concrete from freezing, it is usable under cold temperatures concrete work.
Extra Rapid Hardening Cement:
Calcium chloride, as well as rapid hardening cement, is mixed to make extra quick hardening cement. It is mandatory that concrete produced by utilizing relatively fast hardening cement be carried, poured, compressed, and completed in less than 20 minutes.
The settling, as well as hardening reaction, is catalyzed with extra rapid hardening cement. In quite a brief period following placement, a substantial amount of heat emission occurs. Because of the fast settling, stiffening, and release of such an enormous amount of heat during the early stages of hydration, this type of cement is optimal for winter season concrete work.
Properties of rapid hardening cement
Here’re some distinguished and unique properties of rapid hardening cement:
- Initial Setting Time: It has an initial Setting Time of fewer than 30 minutes. Whereas Ordinary Portland Cement has an initial setting time of more than 30 minutes. It is mostly around 45 minutes or so.
- Final Setting Time: Whereas the final Setting Time is less than 600 minutes.
- Strength gain: It gains strength at a faster pace. You can expect to achieve seven days strength in only three days with this type of cement.
- Fineness: The specific surface area of Rapid Hardening cement is more significant than 3250 cm2/gm. In ordinary Portland cement, we grind clinkers to have a specific area of only about 2250 cm2/gm. So, you can compare how fine we tend to make.
- Weight: RHC is lighter than OPC.
- Curing Period: The curing period for RHC is less.
- The heat of Hydration: Because of the early hydration reaction, you can expect to deal with the high heat of hydration. Thus, we don’t recommend this type of cement for mass concreting like dam foundation.
- Soundness: For soundness with Autoclave, the expected value is 0.8%, while with Le-Chaterlier’s apparatus, it goes around 10mm.
Advantages
- Utilizing a large amount of moisture during the cement hydration, RHC faces a low shrinkage pace during the drying process. As an outcome, concrete structures with less porosity emerge to avoid cracks in the cemented form and the impact of moisture over the infrastructure.
- Chemical impacts such as sulphate have little to no effect on RHC properties, and as an outcome, the construction is highly durable and requires minimal maintenance.
- Time is valuable in the building sector. RHC structure solidifies in a proportionate stiffness during a brief period, which is how RHC ensures that the construction speed is rapid.
- Since RHC demands minimal curing time, it indicates that the finalized building work will consume less water volume, maintenance, and investment.
- Minimal carbon dioxide emission occurs during the manufacture of RHC. As a result, RHC is deemed safer and more efficient.
- High temperature and a minimal amount of fuel are required in the dry manufacturing process to make the RHC manufacturing method most economical and cost-effective.
Disadvantages
- RHC is not a preferable option for water retention or submerged infrastructure like reservoirs and dams. RHC is a hydrodynamic concrete that produces a lot of heat during the hydration process. Microcracks can form as a consequence of this quick cement hydration in the presence of a large amount of moisture. With time, this might lead to corrosion in the reinforcements and lower the substantive structure’s durability.
- RHC must be disregarded during mass concreting huge concrete buildings because it generates a lot of heat. As a result of the large temperature gradient between the external and internal components of the structure, fractures appear.
- The RHC is costly to utilize for construction works. Therefore it is not a preferable option.
Manufacturing
Companies rely on the dry process of cement manufacturing for the rapid hardening of the cement. The famous brand is Ultratech Rapid Hardening Cement.
Anyhow, for this type of cement, we use limestone and shale as the raw material. We heat raw material in extremely high temperatures. Once they take the shape of clinkers, we mix them with a small amount of gypsum. Afterwards, we grind them to a fine powder to get the final product of rapid hardening cement.
Recommended for you: Specific Gravity of Cement Test
Difference between rapid hardening cement and quick setting cement
The main difference between rapid hardening and quick setting cement is the gain of strength. Quick setting cement only sets quicker but doesn’t gain strength. By strength, we mean the ability to withstand on its own without the aid of the external formwork.
In the case of rapid hardening cement, the fast rate of gain strength allows you to remove formwork, but at the same time, you can set the concrete structure to service under loading.