Water is an important ingredient of a concrete mix and water cement ratio is an important factor in concrete or cement mix design. While working at site, concrete workers always try to add water in it so as to increase the workability of concrete but actually they are reducing the strength and durability of concrete.
As per the common definition of water-cement ratio:
“It is the ratio of weight of water to the weight of cement in the concrete mix”
Duff Abrams, an American researcher from Illinois has carried out a detailed research on composition of concrete mixes and from there derived the impact of water-cement ratio. So, it was the first time in 1918 the term water-cement ratio was evolved as a contributing factor towards workability, strength, durability, and slump of concrete.
Concrete is a macro-mixture of ingredients that are suitably mixed in specified proportion to makeup a plastic paste called concrete. The proportion of concrete ingredients is very important that defines various properties of concrete including, compressive strength, slump, setting time, heat of hydration, and VeBe time.
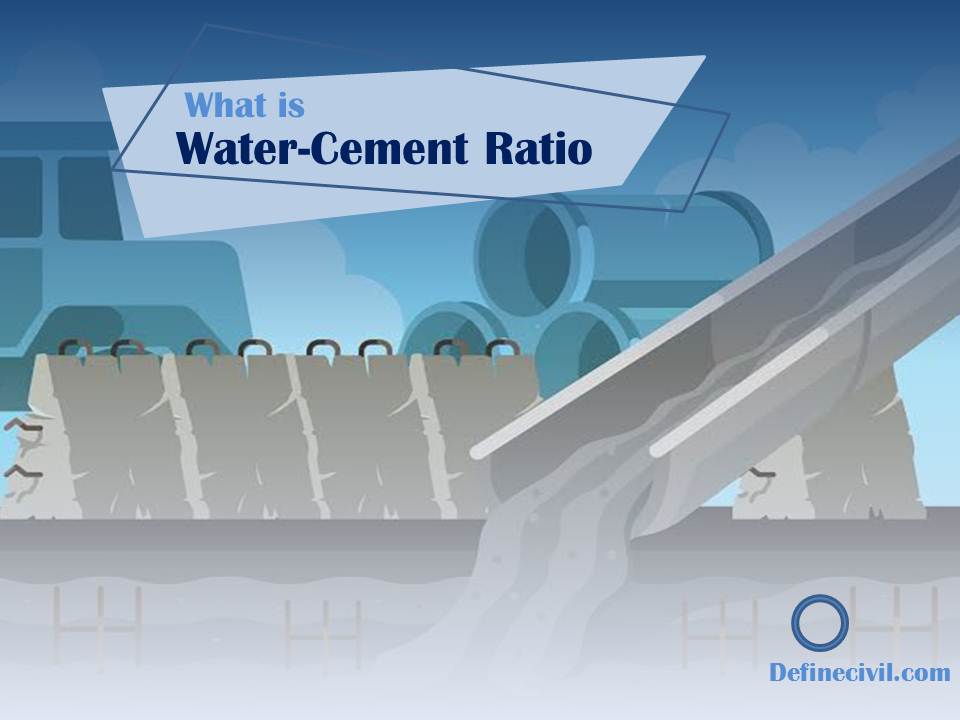
Requirement of Water
Water is not only required for the hydration reaction of cement but it is also a contributing factor in making concrete mix workable and plastic. It is a well-known fact that the minimum amount of water required for the hydration reaction of cement is 0.35. This means, for each kilogram of cement you required 0.35 kg or 0.35 liters of water to hydrate it completely.
But as I used the word – “minimum” so definitely a concrete mix with w/c ratio of 0.35 may not mix thoroughly. So generally for normal concrete mixes, a water-cement ratio of 0.45 to 0.60 is selected during mix design. IS code 10262 of 2009 also quotes the ratio of 0.4 to 0.6 for all normal concrete mixes like M10, M15, etc.
According to 1997 Uniform Building Code, the water to cement ratio should be maximum of 0.50 for concrete exposed to freezing and thawing or moist condition or to deicing chemicals. Whereas, for concrete with severe or very severe sulfate condition should have maximum value of 0.45.
Relation between water & Strength of concrete
If we look at the relationship between water cement ratio and compressive strength of the concrete; it is easy to understand that a decrease in water cement ratio increases the compressive strength in a non-linear (second degree) relation and vice versa. But there is another factor that is important for field placement and pouring of concrete i.e. “workability”.
[su_box title=”Don’t Forget to Read this article” style=”glass” box_color=”#f64420″]What is workability and the all the factors that effect the workability of concrete. [/su_box]
Workability of concrete not only defines the durability and quality of concrete but is also an important consideration for defining the longevity. So, in cases where a higher strength concrete is required, supplemental cementitious materials like fly ash, slag, silica fume, and natural pozzolans can be added to increase the strength, reduce heat of hydration, and make concrete mix more workable. The effect of excessive water on the strength of concrete is illustrated in the figure below:
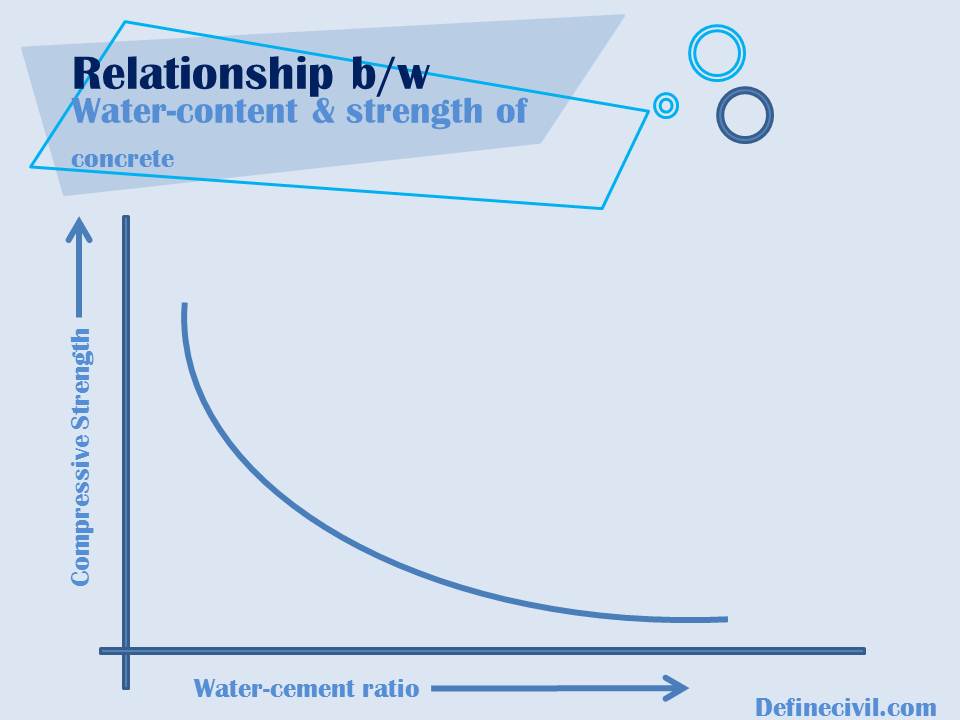
Effect of Excessive Water Content on concrete mix
So now you might be asking that why we can’t increase the water content? Actually, increasing the water content not only reduces the strength of the concrete but it also increases the chances of segregation of the concrete mix components i.e. aggregate, sand, and cement paste. The concrete mix in such cases can result in bleeding, microscopic pores and there would be even more shrinkage cracks.
Also Read: Difference between Segregation and Bleeding in Concrete
Sand or fine aggregate is a filler material that just creates an effective concrete mix that can take the load easily without crumbling. JXSC sand maker are one of the best in the market.
How to calculate Water-Cement Ratio?
This is actually a common question but water-cement ratio is not a thing to calculate. You have to select it from various workability tests while selecting the aggregates and during mix design. For normal mix, you can use Table 5 for the Water-cement content of the IS 10262 (2009) code to select minimum value based on the exposure of concrete structure.
Now lets see how we can calculate the value of mix design contents from the water-cement ratio.
For a 50 kg cement bag the amount of water required would be as follows:
Required quantity of water = W/C ratio X volume of cement
Thus the required quantity of water = 0.55 x 50 kg = 27.5 kg or 27.5 liters
(as density of water = 1000 kg/m3)