While working on masonry projects, there’re number of times you need a Concrete block calculator to help you calculate concrete blocks needed to build a wall.
Whether you’re laying a new wall or are replacing a brick wall with a concrete block, this online calculator help you estimate the number of blocks required as well as deciding the right size of block for your walls.
This calculator works for all type of concrete blocks:
- Cinder blocks – CMU blocks
- Concrete bricks
- Hollow core blocks
- Solid blocks
- Reinforced concrete blocks
For estimating quantity of bricks in a wall; here’s the other guide about estimating quantity of bricks in a wall.
Features of the calculator
Size of block
You can either choose from the standard cinder block sizes commonly used in U.S.A or you can also choose a custom size. For that you need to enter the height, width, and thickness of the block.
If you want to know the standard sizes of bricks, read the article here about brick sizes.
Mortar joint thickness
You can also specify the thickness of the mortar joint (but that’s optional, the preset value of mortar joint in concrete blocks is 3/8”. Recommended size is ¼” to ½”.
Opening deductions
There’s no other calculator online offering this feature. Obviously if you’re working on block masonry wall that has some kind of opening like doors or windows; you’ve got to deduct that area from the project to estimate the right quantity of block work.
So, with this calculator you can easily enter the dimension of windows and doors to deduct the quantity from the overall value.
You just need to check or tick the deductions area and it will let you enter the size of opening as well as numbers.
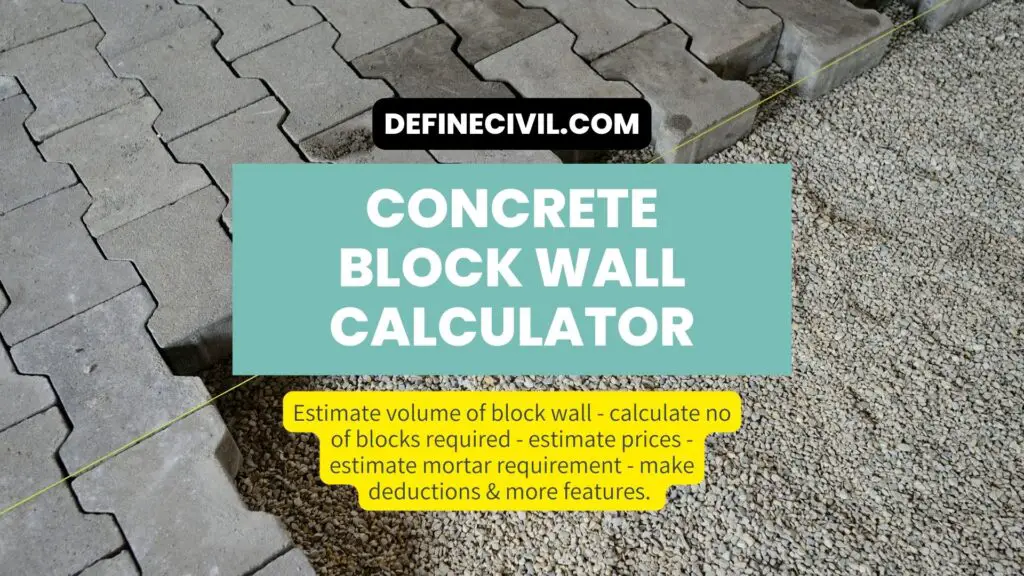
Mortar material estimate
It also let you estimate the material required for laying and jointing the block work. It features two types of mortars here. If you’re using a standard mortar bag; you’ll get the estimate for number of bags of mortar required.
If you’re choosing to make mortar manually by mixing cement and sand; you can choose the right ratio of the mortar mix to calculate required quantity of cement and sand.
Price Estimate
The calculator also helps you estimate the price of the entire block masonry project. If you’re a contractor and looking to bid on concrete block project; this is a very useful feature. You can just enter your project specs in the calculator and it will help you estimate a range of minimum and maximum cost so you can choose the right price for bidding.
This also helps you prepare an accurate quote in matter of few seconds to inspire your prospect client.
The Concrete block Calculator
How do you calculate a CMU block?
A lot of residential and commercial construction projects rely on CMU because they offer good thermal insulation, are effective in absorbing sound and are faster to construct. CMU blocks are also stronger than typical brick masonry.
However, estimating CMU blocks is different than the typical brick masonry. The sizes of cinder blocks are different, and the typical quantity of mortar used for laying is different than stone or brick. Your estimate may change considerably because of different types of block work for your project. Similarly, labor charges, transportation, and reinforcement; there’re a number of factors you need to consider before you can actually bid on a CMU block work.
For calculating the number of blocks required, you can simply estimate the area of the wall or block work. Simply multiply the length of wall with the height of the wall. Divide this area with the size of a standard block (length x height). This will give you the number of blocks needed for a typical wall size.
Also Read: How much does a cinder block weigh?
Here’re some typical steps to calculate the number of blocks you need for a project:
Know the length of the wall
The length of the wall is the longer dimension. If you are on site working on some replacement or demolition project, you can measure the length physically using meter tape.
If you have drawings or blueprints, you can simply use that to determine the length in units of feet or meters.
Know the height of the wall
Height of the wall is from the floor top level to the tip of the ceiling. For foundation it will be the height above the concrete lean concrete and above the floor level.
Choose the size of the block (length x height)
Here’s a detailed guide about different sizes of concrete blocks. The nominal size of the block includes the mortar joint thickness while the actual size offered by the suppliers is slightly less to accommodate for the mortar joints. So, it is very important to choose the right size of blocks work.
We use the actual size in our calculator to make it easy for deciding the mortar joint thickness based on your project requirements.
The most common size of concrete block is 8x8x16 (depth x thickness x length) .
Calculate the area of the wall
The next step is to multiply the length with the width to determine the area of the wall. If you have any openings (windows or doors) you can determine the area of these deductions and subtract that from the wall area.
Note: 1 feet = 12 inches
Gross Area of wall = length in inches x height in inches
Deductions of windows = (length of window x height of window ) x no of windows
Deduction for doors = (length of door x height of door) x no of doors
Net area of wall = gross area – deduction of windows – deduction due to doors
Calculate the number of blocks required
Now you can divide the net area of the wall with the standard block size to get the number of blocks required for the wall.
No of blocks required for a wall = net area of wall in sq. inches/ standard size of block (8” x 16”)
Estimate the quantity of mortar required
On average, for laying 100 concrete blocks you required three bags of cement. If you are using pre-mixed bags of mortar, you need 80 pound bag to cover 12 blocks.
CMU Masonry Estimation Basics
A typical concrete masonry unit (CMU) involves using rectangular concrete blocks for making structural as well as partition walls in residential and commercial construction. These cinder blocks or concrete blocks are either solid or have a hollow core with a different set of applications.
It is a versatile building material that can be stacked easily to form a robust retaining wall or a part of a building. Cinder blocks are also used to form foundation walls or stem walls and have numerous advantages over typical concrete poured walls. In foundation work, the hollow cores of the blocks are reinforced with rebar embedded in concrete.
Also Read: Basics of estimation process
Material takeoff for CMU Block work
There’re two methods to undertake CMU block takeoff, and each method has its own pros and cons:
- The surface area method
- Volume method
Note: Volume method is only recommended if your project includes block wall with different thicknesses.
Also Read: Different quantity surveying methods
In the surface area method, we determine the area of all walls one by one by multiplying the height and length of the wall. From this area, we can subtract the area of the openings like ventilators, doors, and windows. In the end, we can divide the net area by the standard area of a CMU block to get the number of blocks required for a wall.
In the volume method, we can either take the area of all masonry work from the plan or measure the length from the blueprints and multiply it with standard widths to get the area. We multiply this area with the total height of the wall to get the volume of the block masonry. In the end, we can subtract the volume of any openings as we just did in the area method. For estimating the number of blocks, you can simply divide the net volume with the volume of standard block work.
Wastage
For CMU blocks, there’s always going to have some wastage of materials. There’re cut pieces along corners, or you might have some damaged pieces while shifting or handling at the site.
So, it is always good to include 3 to 4% as wastage in your material estimate for masonry work.
Adding labor charges
Most of the block masonry projects follow the per square foot method, but it is pretty important to thoroughly read your bidding instructions before taking off the quantities. But along with the block work, you need to include the amount for mortar and any other material in the project, like concrete for filling cores, as well as reinforcement.
After you have obtained the material cost of the project, you can determine the labor charges.
Generally, the contractor’s cost for labor is between $10 to $17 per square foot or an hourly rate of $34 to $100 per hour.
Add a percentage for extras.
Depending on the nature or urgency of the job, you might need to hire more labor to accomplish the job early. Similarly, there’re more risks involved in working at heights than working on a ground floor. So, you need to include all such impacts while preparing a bid for the CMU block masonry.
Also, you might have labor or two who can get sick or injured at work. That’s why it is important to add a 5 to 10% margin in your bid estimate to take care of the delays or any unforeseeable circumstances.
Add overheads and profit margins.
It is now the most critical part of your bid. You’re operating a business, and as a contractor, you may have business overheads like advertising, utility bills, car repairs, and staff members.
So, while bidding on any job, you need to include a factor of a small number of your expenses in every job. If you have already determined your monthly operating expenses, you can determine the overheads for your project by multiplying the month’s budget in days with the duration of your masonry work.
After adding all the labor costs, operating expenses, and equipment costs, you can add a profit margin at the end. Your profit margin depends a lot on your experience, availability of work, and your cash flow.
If you’re new in the field and don’t have any continuous stream of projects, you can set a profit margin of 5%. Otherwise, 10 to 15% is also common.
Further Read: Block wall foundation requirements