Fiber-reinforced concrete also referred to as FRC is a type of concrete that contains fibrous material to improve structural strength. It is made up of short distinct fibers that are evenly dispersed and orientated randomly.
The fibers we use in concrete are small distinct piece of reinforcing material that possesses certain characteristic properties. In general, we identify fibers based on their aspect ratio which is the ratio of their length to diameters. The fibers we typically use in concrete have aspect ratio of 30 to 150.
The most common types of fibers we use in concrete are steel fibers, glass fibers, natural fibers, and synthetic fibers. The characteristics of concrete changes with varying concretes, fiber materials, geometrics, distribution, and orientation.
One of the most common applications of fiber reinforcement is in shotcrete. However, we can use fiber reinforced concrete for diverse applications like floors, ground pavements, and parking areas.
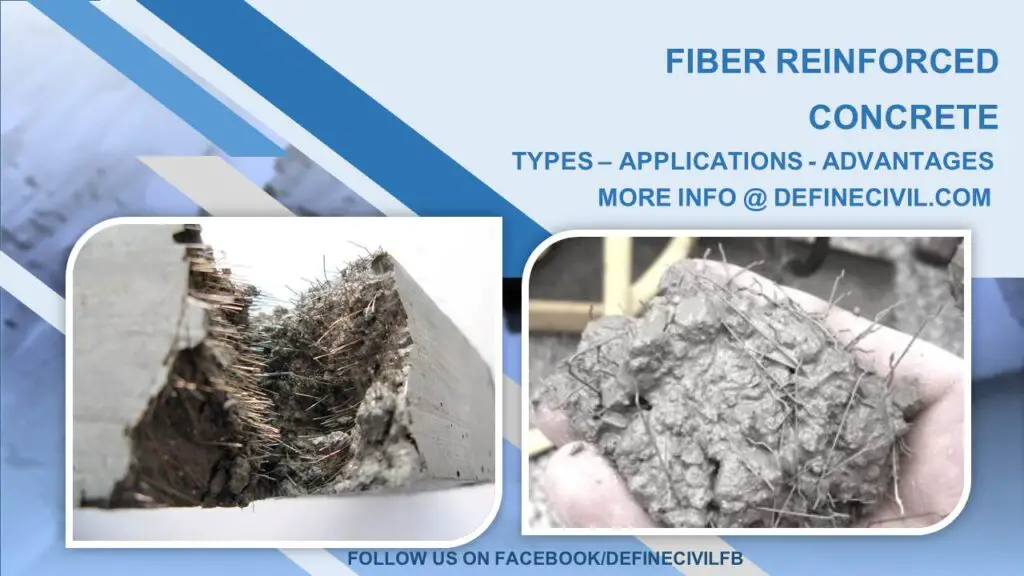
What is fiber reinforced concrete?
Concrete seems to have great compressive rigidity but is surprisingly weak in tension. Hence it is frequently supplemented with substances that are robust in tension like rebar.
Use of steel bars for normal concrete have evolved and been explored for quite some time. It is now so common that now we can’t even imagine a concrete structure without tensile reinforcement.
The employment of fibers as reinforcements is rather a relatively new invention. Engineers use fibers to enhance the tensile strength of conventional concrete as well as to adapt to a variety of particular structural concrete purposes.
But remember the fibers are not used as a replacement of the tensile reinforcement. However, you can still reduce the temperature or shrinkage reinforcement because of the extra tensile strength from the fibers.
What is the purpose of fiber reinforced concrete?
One of the most obvious reasons of using fibers in concrete is to control shrinkage cracks and drying shrinkage cracks. You can also use it on water bodies like ogees or spillway structures where there is a greater impact of abrasion and shatter. It reduces the permeability of concrete by avoiding bleeding of cement slurry.
Where is the fiber reinforced concrete used?
This fiber reinforced concrete are now in use for practical projects. Engineers use them in runway, pavements, and aircraft parking. In fact, it might have been the best option for slope stabilization. Because of the enhanced durability, this type of concrete is best for hydraulic structures like dams and barrages.
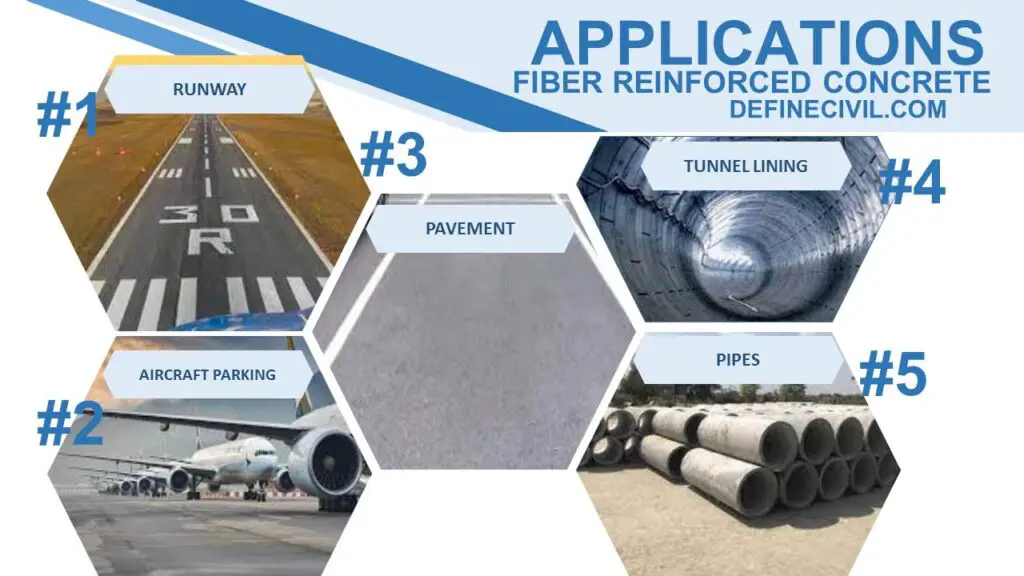
So, this brings us to where we should talk about the different types of fiber reinforced concretes.
Let’s delve in.
Types of Fiber-reinforced concrete
Fibers, in particular, have been shown to improve concrete’s crack resistance, flexibility, and longevity. The numerous types of fibers often utilized in the building industry are listed below.
-
Steel – Fiber Reinforced Concrete:
- The most prevalent type of steel fiber is round steel fiber, which is made by breaking round wires into small strips.
- The normal diameter is between 0.25 and 0.75mm.
- Isolated fibers tend to gather in the mesh, making uniform distribution problematic. Introducing fiber bundles, which split during the blending process, can help to avoid this.
-
Polypropylene – Fiber Reinforced Concrete:
- Polypropylene is among the most affordable and widely available polymeric materials.
- Polypropylene fibers are impervious to most chemicals and it is the cement-based matrix that deteriorates first when exposed to harsh chemicals.
- Since polypropylene composites are hydrophobic, they are easy to mix because they do not require continuous exposure and merely need to be uniformly disturbed in the mix.
- Commercially accessible polypropylene shorter fibers with low volume proportions ranging from 0.5 to 15 are utilized in concrete.
-
Glass – Fiber Reinforced Concrete:
- Glass fiber consists of 200 to 400 distinct filaments that are loosely linked together to form a stand.
- Such stands can be cut to different lengths or connected to create fabric mats or tapes.
- Glass fiber has mostly been employed to reinforce the concrete or cement matrix used in the manufacture of thin-sheet items.
- E-glass is a type of glass fiber that is widely utilized.
-
Asbestos – Fiber Reinforced Concrete:
- Asbestos, a naturally occurring and affordable mineral fiber, has indeed been effectively mixed with Portland cement mixture to produce asbestos cement, a commonly used commodity.
- Asbestos fibers are useful for sheet item pipelines, tiling, and curved roofing parts because of their thermodynamic, mechanical, as well as resistance to chemical attack.
- Unreinforced matrices are between two to four times the costs of asbestos cement panels.
- The fiber, however, has moderate impact resilience due to its short size (10mm).
-
Carbon – Fiber Reinforced Concrete:
- Carbon fibers are the most modern and, most likely, the most stunning contribution to the spectrum of commercially accessible fibers.
- Carbon fiber has extremely high flexibility and splits tensile modulus. These are quite large.
- Nevertheless, steel’s persistence and stiffness attributes are higher.
- However, because they are more prone to deterioration than even glass fiber, they are usually coated with resin.
-
Organic – Fiber Reinforced Concrete:
- Steel and glass fibers are chemically highly inert unlike organic fibers like polypropylene or even natural fiber.
- They are also less expensive, particularly if they are organic.
- To make multiple breaking composites, a considerable amount of vegetable fiber might be utilized.
- A superplasticizer can be used to overcome the problem of blending and homogeneous dispersion.
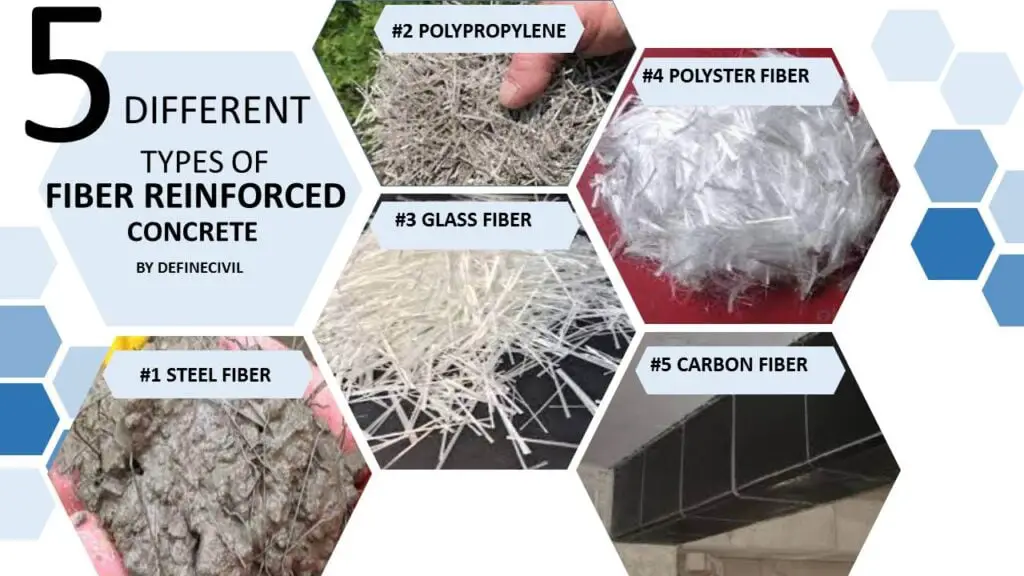
Properties
- Flexural power was observed to be 2.5 times higher when 4 percent of fibers were used.
- FRC has a hardness of 10 to 40 that exceeds that of ordinary concrete.
- Separating Tensile Properties: It has been found that adding 3% fiber by weight to mortar increases its splitting tensile capacity by 2.5 times that of non – reinforced cement.
- Fibrous cement has strength properties of 5 to 10 times that of conventional concrete, based on the proportion of fiber employed.
Is fiber reinforced concrete worth it?
- It improves the concrete’s tensile strength.
- It minimizes the water and air spaces in the gel’s natural porosity.
- It improves the concrete’s longevity.
- Reinforced concrete is a hybrid product in which the reinforcement serves as the reinforcing fiber while the concrete serves as the matrices. It is also critical that now the two substances behave similarly under thermal loads so that divergent malformations of reinforcement and concrete are minimized.
Applications
- FRC is utilized in the construction work and maintenance of dams, reservoirs, and other water storage structures to protect them from cavitation and extreme erosion due to massive waterborne debris.
- Industrial machinery frameworks, lighting rods, water, and oil containers, and concrete restorations are among them.